Whether it's transforming a steel plate into a complex gear, creating a high-performance fiber material into a sleek vehicle shell, or simply cutting a specific type of blank with precision, none of these tasks can be done without the help of a machine. This particular kind of machine, which is used to create other machines, is known as the "mother machine" of the industry. With the progress of industrialization, its control methods have transitioned to digital control. Digital machine tools are considered the cornerstone of industrial modernization, and their technological level reflects the comprehensive competitiveness of a nation.
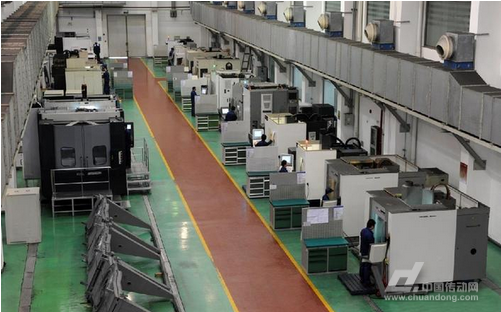
To strengthen the foundation of China's industry and reduce the gap between China's CNC machine tools and those of the international community, China officially launched the "High-end CNC Machine Tools and Basic Manufacturing Equipment" national science and technology major project in 2009. Over the past eight years, significant progress has been made, with output value increasing by about 70.6 billion yuan. The technical level of China's high-end CNC machine tools has continuously improved, providing strong support for domestically produced equipment in key sectors. Breakthroughs have been achieved in the localization of high-end CNC machine tools.
Significant Increase in Manufacturing Capacity
Through the development of CNC lathes with high demand and large imports, China's machine tool companies now have independently developed products that can compete with imported equipment, improving their design and manufacturing capabilities.
"On a machine tool, X-axis motion can process lines, adding the Y-axis allows for surface processing, and with the Z-axis, you can handle three-dimensional objects," explained Wang Decheng, Director of the Machinery Science Institute, to reporters. "But this is far from sufficient." He further noted that industries often require processing of more complex surfaces, and the materials, structures, and processing techniques for many critical components in ships, aircraft, rockets, satellites, and spacecraft have unique characteristics and challenges that cannot be addressed by traditional methods. To meet these demands, multi-axis linkage, high-speed, and high-precision CNC machine tools are necessary.
Wang Decheng emphasized that multi-axis linkage is a crucial technology in CNC machine tools. It enables simultaneous movement across multiple coordinate axes of a machine tool, allowing the tool or workpiece to be coordinated and controlled simultaneously under the CNC system, thereby completing complex shape processing. Although China is currently the world's largest manufacturer, the lack of such high-end CNC machine tools limits our control over high-end manufacturing.
"In the past, we couldn't produce five-axis linkage machine tools, and the CNC systems used were also manufactured abroad. To manufacture a component for a large ship, many manufacturers would scramble to use just one imported machine tool. For aerospace companies, foreign high-end CNC machine tools not only restrict our imports but also, even when imported, their CNC systems have information backdoors, posing a significant threat to national defense security," said Lu Bingheng, a special technical engineer and Academician of the Chinese Academy of Engineering.
With the rapid development of China's aerospace, shipbuilding, energy, power, defense, automotive, and construction machinery industries, the demand for large-scale, heavy-duty, composite, high-precision high-end CNC machine tools has surged. Addressing the current situation of high-end CNC machine tools is urgent.
In this regard, the "National High-end CNC Machine Tools and Basic Manufacturing Equipment" national science and technology major project has focused on deploying large-scale imported machining centers and CNC lathes with significant market demand. Machine tool companies have developed numerous new products that meet market needs. Technologies like gantry machining centers and 5-axis machining centers have matured. The performance of heavy-duty forging equipment approaches the international advanced level. Precision horizontal machining centers possess independent intellectual property rights. Core technologies for flexible manufacturing systems have been developed. By the end of the Twelfth Five-Year Plan period, the product design and manufacturing capabilities of China's machine tool companies have significantly improved, and the international competitiveness of high-end CNC machine tools and equipment continues to grow.
In the field of high-end numerically-controlled machine tools, China has finally developed independently produced products that can compete with imported equipment. The successful development of heavy-duty forging and CNC punching equipment, such as 80,000-ton large-sized die forging presses and 10,000-ton aluminum sheet tensioning stretchers, has been completed. These developments have enabled domestic aviation to adopt large-scale integral forming technology. Large tank complete welding equipment was successfully applied to the development of new-generation rockets like the Long March V, and the first production demonstration line using domestic processing centers and CNC turning centers was established in the aerospace field. More than 100 types of new-generation launch vehicles, docking mechanisms, lunar exploration projects, and over 10,000 critical complex parts have achieved remarkable economic and social benefits. The industrialization of CNC forging and forming equipment has achieved remarkable results. Among them, the auto cover press line has a domestic market share exceeding 70%, with a global market share surpassing 30%, effectively promoting the autonomy of domestic auto equipment and successfully exporting 9 vehicle production lines to the United States.
Technical Standards Gradually Improved
China's machine tool industry has formed a large number of technical standards and specifications. Some of these standards have been included in international standards. The industry's international competitive advantage has significantly strengthened, providing strong support for product development.
Since the implementation of the National Science and Technology Major Project on "High-end CNC Machine Tools and Basic Manufacturing Equipment," the industry's technical level has significantly improved. Lu Bingheng introduced that more than 30 key products, such as precision horizontal machining centers, developed by China have reached the international advanced level. Among them, the 25-meter vertical column turning vertical milling lathe is a high-end product urgently needed for the construction of major national engineering projects. Its technical parameters and technical grades rank among the world's leading, with the largest machine specifications and bearing weight globally, representing the highest level of CNC heavy machine tools in the country.
What is most noteworthy is that the independent innovation and reliability of China's machine tool industry have significantly improved, and standards and technical specifications have gradually improved. Through special implementation, domestic machine tool backbone enterprises and universities and users have jointly developed, and the establishment of national/industry standards for the reliability evaluation of CNC machine tools in the machine tool industry has been actively promoted. The average time between failures of the machine tool host has increased from 400 to 500 hours before the implementation of the special project to approximately 1200 hours, and some products have reached the internationally advanced 2000 hours.
Lu Bingheng introduced that the special achievements formed a large number of technical standards and specifications. Some of the technical standards were taken seriously by international counterparts and included in international standards. The industry's international competitive advantage has significantly enhanced, providing strong support for product R&D and contributing to the continued development of the national equipment manufacturing industry. The improvement of capabilities plays a safeguard role.
At the end of 2016, the S-shaped test piece standard for testing the accuracy of 5-axis linkage machine tools independently proposed by China passed the examination and approval by the International Standards Committee, becoming China's first standard in the field of high-end CNC machine tool design and testing, achieving a "zero" breakthrough.
In addition, for more than eight years since its special implementation, 3956 invention patents have been applied for, 407 national and industry standards have been established, and 2,951 new products and technologies have been researched and developed. In industry research institutes and key enterprises, 18 innovation capability platforms have been built, 70 demonstration projects have been deployed, and more than 5,500 innovative talents have been trained.
Domestic "Brain" Fills the Gap
The CNC system has achieved a leap from analog, pulse to full-digital bus, initially possessing the competitive ability with similar foreign products, and breaking through the bottleneck that restricts the development of the CNC machine tool industry in China.
The CNC system is the "brain" of machine tool equipment and is the key factor determining the functionality, performance, reliability, and cost of CNC machine tools. It is also the bottleneck restricting the development of the CNC machine tool industry in China. The weak foundation and "mindless brain" have always been the shortcomings of "Made in China."
According to experts, CNC systems, servo motors, servo drives, etc., are the most important and critical basic components of manufacturing equipment. To achieve the goal of "Made in China 2025" and form the core competitiveness of "China's wisdom," it is inseparable from the innovation of key technologies such as servo drives and servo motors in CNC systems.
To make up for the shortfall, the deployment of the "National High-tech CNC Machine Tool and Basic Manufacturing Equipment" major national science and technology projects implements the entire industry chain, and the domestic CNC system achieves the original surpass of some technologies. The company has mastered the hardware and software platform design and mass production technology of the CNC system, reaching the international mainstream product technology level in key technical indicators such as multi-channel, multi-axis linkage, and high-speed interpolation.
Through special support, China's numerical control system has achieved a leap from analog, pulse, and all-digital buses, and has initially had the ability to compete with similar foreign products. The high-end numerical control system, functional components, and host product supporting R&D have initially achieved batch support with high-end numerical control machine tools. According to Luo Junjie, Deputy Director of the Equipment Industry Department of the Ministry of Industry and Information Technology, in 2016, the numerical control machine tool dedicated to the research and development of high-end numerical control systems had accumulated more than 1,000 sets of sales, and the domestic market share increased from less than 1% before the special start to about 5%.
Currently, the domestic high-end numerical control system has been matched with more than 10 types of more than 600 high-grade CNC machine tools and has begun to be applied in key aerospace enterprises. "The quality of functional parts and enterprise products has steadily improved, the series of products has been continuously improved, the testing equipment for rolling functional components has been built from scratch, and the key technical indicators such as static stiffness and the level of test equipment have ranked among the top in the world. As of now, the market share of rolling functional components in high-end CNC machine tools reaches 20%, which is four times higher than that before the implementation of special projects in 2009. The variety satisfaction rate is 80%," said Luo Junjie.
Lu Bingheng stated that China's CNC machine tools will focus on two key user areas: aerospace, automotive, and common technology research and emphasis on process verification in key areas; the development of key core components and industrialization will be paralleled; accelerating the development of innovation capability platforms and demonstration projects, and strengthening innovative talent training and introduction of high-end talents, focusing on solving problems related to CNC systems and functional components, reliability and accuracy maintenance, processing efficiency, and improvement of process levels, realizing the application of special achievements in scale and complete sets of key areas, and implementing for full implementation of "Made in China 2025" to provide support.
In the next step, CNC machine tools will be closely linked with other national science and technology projects and local science and technology projects to form a concerted effort to jointly achieve the leapfrog development of the national high-end CNC machine tools and basic manufacturing equipment technology innovation competitiveness.
Digital Printing Membrane Switch
Digital Printing Membrane Switch,Embossed Tactile Membrane Switch,Membrane Switch Panel,Membrane Tactile Keypad
CIXI MEMBRANE SWITCH FACTORY , https://www.cnjunma.com